Economie & innovation
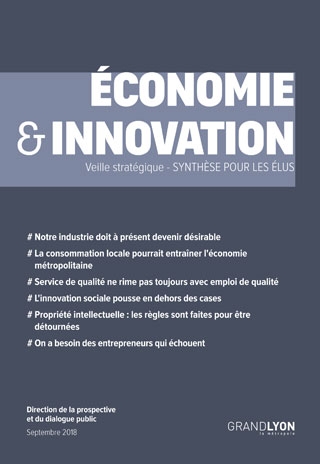
Étude
Veille stratégique - synthèse pour les élus.
Interview de Éléonore Gendry
Après un passage en région parisienne au sein de l’association d’élus Intercommunalités de France, puis de l’établissement public territorial Est Ensemble (93), Éléonore Gendry a mené une thèse en urbanisme consacrée à l’évolution des liens entre la ville et l’industrie dans l’agglomération lyonnaise.
Désormais, elle travaille à l’Université Lumière Lyon 2, dans le cadre d’un programme de recherche sur la ville durable et les bâtiments innovants.
Dans cet entretien, elle nous expose les enseignements de son travail de recherche et met en perspective les enjeux redirectionnels actuels à l’aune du temps long, afin de questionner nos représentations des changements de modèle économique industriel sur les territoires.
Pourriez-vous préciser le cadre dans lequel s’est inscrite votre thèse, ainsi que les thématiques qu’elle aborde ?
Nous avons pu voir que les crises climatiques, sanitaires ou géopolitiques observées ces dernières années menacent les approvisionnements locaux. Pour les autorités locales, la reterritorialisation de la production apparaît donc comme un enjeu essentiel.
C’est en considérant ces nouveaux défis que la Métropole de Lyon, aux côtés de celle de Saint-Étienne, a répondu à l’appel à projets Territoires d’Innovation de Grande Ambition (TIGA), lancé par l’État en 2018 dans le cadre de son troisième plan d’investissement d’avenir autour de la question de l’intégration et de la (re)connexion de l’industrie au territoire et à ses habitants.
J’ai pris part à ce projet en réalisant une thèse au sein de Laboratoire d’Excellence (LabEx) Intelligence de Mondes urbains (IMU) et du laboratoire Environnement, Ville, Société (EVS) qui s’intéresse à l’évolution des liens entre la ville et l’industrie, des années 1950 à aujourd’hui, à partir de l’étude des transformations du travail.
Pour ce faire, j’ai choisi de réaliser une monographie en prenant comme terrain d’enquêtes une industrie lyonnaise représentative d’un modèle de production que l’on peut considérer comme « traditionnel » : le constructeur de véhicules industriels Berliet (aujourd’hui Renault Trucks).
Je me suis plus particulièrement intéressée à son site industriel de Vénissieux/Saint-Priest qui, depuis 1917, se compose d’un centre d’études et d’une usine. Rattaché en 1975 à la filiale poids lourds de Renault, la Saviem, puis racheté par la multinationale Volvo en 2002, Berliet fut l’un des plus gros employeurs de la région lyonnaise, avec près de 20 000 salariés au début des années 1970. L’entreprise disposait même de sa propre cité ouvrière afin de loger son personnel.
Pour appréhender plus facilement les changements du travail chez Berliet, ainsi que les mutations urbaines qui s’y rattachent, j’ai centré mon étude sur l’évolution de la production d’un objet industriel caractéristique de l’entreprise, les moteurs, car ces derniers ont connu de nombreuses évolutions technologiques et réglementaires au cours des dernières décennies qu’il m’a semblé pertinent de mettre en lumière.
Si mon choix s’est porté sur cet objet caractéristique de l’industrie automobile, c’est aussi parce qu’il est encore aujourd’hui en partie produit sur le site de Vénissieux/Saint-Priest, ce qui n’est plus le cas pour de nombreuses autres pièces.
Quelles différences avez-vous pu observer entre les usines moteurs d’hier et celles d’aujourd’hui ?
Dans les années 1950, chez Berliet, la production des moteurs est intégrée, c’est-à-dire que la presque intégralité des tâches de fabrication est effectuée au sein de l’usine de Vénissieux. Les matières premières (sable, coke) sont acheminées par voies ferrées et distribuées au sein de l’usine à l’aide d’une gare de triage présente sur le site de production. Leur transformation en différentes pièces débute dans les fonderies et les forges.
Elles sont ensuite usinées puis assemblées pour former des moteurs. L’intégration concerne aussi les outils de production, que Berliet fabrique en grande partie. À partir des années 1970, dans un contexte d’ouverture des marchés à l’international, certaines pièces spécifiques des moteurs dont la production est coûteuse sont désormais sous-traitées. La grande majorité des composants des moteurs reste toutefois fabriquée sur le site de Vénissieux.
Mais, dans les années 1990, avec l’essor de la mondialisation et donc de la sous-traitance, les activités de forges disparaissent, tandis que les procédés d’usinage se numérisent grâce à des machines à commandes désormais importées. L’usinage des pièces cesse alors au début des années 2000, tout comme les activités des fonderies, et le rachat de l’usine de Vénissieux par la multinationale Volvo à la même période entraîne la restructuration de la fabrication des moteurs Berliet à l’échelle internationale.
À Vénissieux, seules les activités d’assemblage sont maintenues. Elles s’opèrent autour de deux lignes de montage pilotées par des ordinateurs implantés au sein d’une nouvelle usine inaugurée par le constructeur suédois en 2004. Cette usine, que je qualifie « d’usine tournevis », importe ainsi des pièces du monde entier avant de les assembler. Elles sont produites en grande série par des usines Volvo réparties mondialement ou par des fournisseurs.
Les différentes pièces importées sont stockées au sein de grands hangars libérés des anciennes activités de fabrication du constructeur. L’usine moteurs Renault Trucks d’aujourd’hui donne donc à voir une activité productive proche de la logistique.
Quelles ont été les grandes étapes de reconfiguration des chaînes de valeur et donc du travail industriel ?
Dans les années 1950, la production des grandes industries françaises, dont le capital est souvent familial, s’organise autour d’une chaîne de valeur localisée. La plus-value dégagée par les entreprises étant liée à la vente de leurs produits, ces dernières cherchent à maîtriser l’ensemble de leur chaîne de production, de la conception à la fabrication.
Comme j’ai pu l’exposer, les industriels tels que Berliet assurent donc la presque intégralité de leurs activités de fabrication au sein d’usines intégrées, ce qui requiert une importante main-d’œuvre ouvrière. En 1955, l’usine Berliet de Vénissieux emploie ainsi près de 9 000 ouvriers. Les activités de conception sont quant à elle plus restreintes et effectuées par des ingénieurs et des dessinateurs beaucoup moins nombreux. À titre d’exemple, on ne recense que 300 ingénieurs en 1955 sur le site de Vénissieux.
À partir des années 1970, la mondialisation du commerce et l’expansion des technologies numériques complexifient la chaîne de valeur. Comme j’ai pu l’observer chez Berliet, ces transformations participant à l’ouverture du capital des industries, elles complexifient leur gouvernance et donc la chaîne de valeur. À cela s’ajoute l’arrivée de nouvelles exigences techniques et réglementaires qui modifient l’extraction de la plus-value, dorénavant corrélée aux innovations proposées par des industriels qui cherchent à se différencier de leurs concurrents.
Afin d’augmenter leur plus-value, ces derniers investissent donc leurs activités de conception. Anticipant ces évolutions, Berliet fait construire l’un des plus grands centres de recherche et développement d’Europe en 1962. Il en résulte une importante augmentation du nombre d’ingénieurs, de techniciens, mais aussi d’employés (pour répondre à la bureaucratisation de l’activité) dès les années 1980.
À l’inverse, la maîtrise de l’ensemble des procédés de fabrication n’étant plus la principale source de revenus pour l’industrie, la sous-traitance s’accentue, facilitée par l’essor du libre-échange dans des pays où la main-d’œuvre est moins coûteuse. On observe alors des systèmes productifs fragmentés, organisés en « chaînes de valeur globales », qui connectent de nombreux sites à travers le monde.
Cet éclatement de l’activité productive va de pair avec une nouvelle organisation du travail à l’œuvre dès les années 1990 : le lean manufacturing. Elle vise à réduire les coûts de fabrication en limitant les temps de stockage à l’aide d’une production en flux tendu. Pour ce faire, l’entreprise ajuste ses effectifs ouvriers grâce à des intérimaires, dont le nombre varie selon le volume de pièces à produire. Mais c’est dans les années 2000 que s’imposent plus particulièrement les principes du lean, dans un contexte où la finance s’industrialise. Dès lors, l’obtention de la plus-value devient dépendante de la circulation des marchandises.
Ne pouvant circuler, l’activité intellectuelle apparaît alors moins rémunératrice et commence elle aussi à être sous-traitée vers des pays où la main-d’œuvre est moins coûteuse, ou à des start-ups qui assurent les risques liés à l’innovation. Cela n’est pas sans effet sur l’activité des cadres, qui diminue à son tour, comme j’ai pu l’observer chez Renault Trucks. Ils étaient un peu plus de 4 000 en 2013 contre 2 600 en 2019.
À l’heure où l’on parle de réindustrialisation de la France, le préfixe « re » marque un désir de retour, mais pensez-vous que cela soit possible dans les formes généralement imaginées de la fabrication intégrée ?
En l’état, au regard de la mondialisation de la production industrielle, cela semble compliqué, du moins si l’on envisage le retour d’une « grande industrie » qui contrôlerait toute la chaîne de production, « du lingot au produit fini ». En effet, l’éclatement de l’appareil productif dès les années 1970 a donné lieu à des politiques industrielles de spécialisation dans de nombreux pays. Par conséquent, certains procédés de fabrication et/ou filières ont été délocalisés à l’étranger auprès de fabricants/sous-traitants spécialisés.
On pense bien évidemment à la filière textile, mais on peut aussi citer dans le cas de l’industrie automobile la délocalisation des activités de fonderie dans des pays comme la Turquie. Dans l’hypothèse où ces activités — aujourd’hui sous-traitées dans des régions où la main-d’œuvre est peu coûteuse et la réglementation environnementale moins contraignante — seraient réimplantées localement, la question de leur acceptabilité sociale se pose. Sommes-nous prêts à payer plus cher un objet localement produit ? Accepterions-nous la réimplantation de certaines activités polluantes à proximité de nos lieux de vie ?
À ces questionnements s’ajoutent ceux de savoir-faire industriels qui semblent s’être progressivement perdus. J’ai par exemple pu observer au sein de l’usine moteurs de Renault Trucks à Vénissieux que les compétences requises par les ouvriers ne concernent plus une spécialisation particulière, mais plutôt une capacité à s’adapter.
Il en résulte un recours à de nombreux intérimaires, dont la formation ne prend que quelques jours, contrairement à celle des ouvriers d’antan. La perte des savoir-faire concerne aussi la recherche et le développement dans les grands groupes industriels qui, comme nous l’avons vu, externalisent certaines tâches à l’étranger.
Ces propos sont toutefois à nuancer. La France, et en particulier l’agglomération lyonnaise, présente une position stratégique, des infrastructures performantes et une main-d’œuvre parfois très qualifiée, sur lesquelles il faut s’appuyer. Si l’ensemble des procédés de la chaîne de production semble ainsi difficilement pouvoir être relocalisé, une partie pourrait l’être, mais sûrement dans une forme différente de celle d’autrefois et qui reste à définir.
Votre thèse met en avant une évolution de la place de la sous-traitance dans l’industrie. Dans le cadre de votre terrain d’enquêtes, à quelle(s) échelle(s) territoriale(s) s’est progressivement organisée l’externalisation de ces activités de production ?
Le recours à la sous-traitance est peu présent chez Berliet jusqu’aux années 1970. Lorsqu’il existe, il prend souvent la forme d’une collaboration technique entre les bureaux d’études du constructeur lyonnais et ceux de ses fournisseurs.
Ce fut par exemple le cas au début des années 1960, avec la fabrication des vilebrequins dont l’outillage nécessaire à leur fabrication rendait onéreuse leur production en quantité restreinte. Berliet s’est donc rapproché du fournisseur Mavilor, implanté dans la Loire à 35 km de Vénissieux, pour obtenir des vilebrequins.
On peut aussi citer les Ateliers de mécanique du Centre (AMC), situés dans la région clermontoise, qui fournissaient les pompes à huile des moteurs, ou encore l’usine Sigma, autrefois implantée à Vénissieux, qui produisait des pompes à injection pour Berliet. Au début des années 1970, bien que la sous-traitance s’accentue chez Berliet, celle-ci reste régionalisée avec des fournisseurs implantés dans un rayon de 100 km autour de l’usine de Vénissieux.
Mais, à la suite de la fusion entre Berliet et la Saviem, le constructeur lyonnais se voit contraint d’appliquer la politique d’achat de la marque au losange, qui préfère recourir à des partenaires européens (Allemagne, Royaume-Uni, Italie) dans un contexte où le libre-échange prospère. La sous-traitance s’européanise alors, affectant les anciens fournisseurs locaux de Berliet, fortement dépendants de ce dernier.
Au début des années 2000, le rachat de l’entreprise par Volvo mondialise la production. Une partie des activités de Vénissieux est transférée dans les usines du constructeur suédois (Suède, Brésil, Inde, États-Unis) ou auprès de fournisseurs mondialement implantés qui fabriquent des pièces en grande quantité pour la multinationale.
L’externalisation des procédés de production concerne aussi les activités de conception autrefois exercées à Saint-Priest. Certaines d’entre elles ont été redistribuées dans les différents centres de recherche du groupe Volvo, dont l’un d’entre eux a ouvert en 2009 dans la « Silicon valley » indienne de Bangalore.
Volvo fait aussi appel au travail de start-ups mondialement implantées ou à des coentreprises dont il détient une partie du capital comme Cellcentric, importante usine de production de piles à combustible installée en Allemagne. Pour résumer, on est donc passés d’une sous-traitance localisée à une sous-traitance mondialisée.
Votre travail de recherche montre une industrie de plus en plus déconnectée de son territoire au fil du temps. Quelles sont les formes les plus marquantes de cette émancipation selon vous ?
J’y vois plusieurs formes. La plus marquante, selon moi, concerne l’évolution de la gouvernance des entreprises industrielles. Jusqu’aux années 1970-1980, à l’image de Berliet, l’administration des industries demeure largement structurée autour de capitaux familiaux, ou localisée, ce qui favorise un lien fort avec le territoire.
À travers sa politique industrielle et des nationalisations, l’État encourage par la suite la constitution de grands groupes nationaux capables de rivaliser à l’international, comme en témoigne le rapprochement entre Berliet et la Saviem. Mais, cette organisation reste encore pensée à l’échelle nationale.
À partir des années 1990, l’entrée d’actionnaires étrangers et de fonds d’investissement change profondément la logique industrielle. Le capital n’est plus ancré localement : il circule à l’échelle mondiale et cherche avant tout la rentabilité à court terme, sans considérer les besoins spécifiques du territoire. La production, elle aussi, se standardise : les usines et les modes de fabrication deviennent identiques d’un pays à l’autre, selon les principes du lean management, au détriment des savoir-faire locaux et des spécificités architecturales. On trouve ainsi les mêmes usines Volvo en Inde ou en France.
Outre les mutations de la gouvernance industrielle, qui participe à l’éclatement de l’appareil productif, l’émancipation de l’industrie d’avec son territoire s’observe aussi à travers l’évolution de son rôle social. En effet, comme j’ai pu l’étudier chez Berliet, dans les années 1950-1970, les grandes industries ont une place importante dans la vie locale, en participant à la construction de logements pour leurs salariés ou en organisant leur transport.
Si Berliet a érigé une cité ouvrière, il a aussi attribué des aides à la construction à ses salariés pour faciliter leur installation à proximité de son usine. Cette implication diminue nettement à partir des années 1970 et l’arrivée de capitaux extérieurs. Les dispositifs de logement patronaux disparaissent progressivement au profit d’initiatives individuelles ou gouvernementales. Il en est de même pour les services de transport dédiés aux travailleurs de l’industrie.
On amène souvent comme facteur explicatif de l’attractivité d’un territoire les compétences et les ressources humaines dont il dispose. Or vous montrez dans votre thèse un recours accru à l’intérim sur les chaînes de montage et une sous-traitance qui touche même les activités de conception. On a l’impression que le facteur humain n’a pas tant d’importance finalement. Qu’en pensez-vous ?
Il est vrai qu’on observe depuis les années 1990 un recours croissant aux intérimaires pour effectuer des tâches ouvrières. Au sein du site lyonnais de Renault Trucks, ces derniers occupaient 7,44 % des emplois ouvriers en 1995, 26,83 % en 2006 et près de 40 % aujourd’hui.
À l’inverse, les effectifs des cadres au sein de l’entreprise diminuent depuis les années 2010 au regard de l’externalisation d’une partie des activités de conception du groupe. Chez Renault Trucks, ils étaient ainsi 35 % de moins en 2015 qu’en 2013.
Malgré ces évolutions, je ne dirais pas que le facteur humain est devenu négligeable, mais plutôt que les caractéristiques prises en compte se sont transformées. Aujourd’hui, en ce qui concerne les ouvriers, il y a surtout un besoin de ressources humaines adaptables et disponibles sans délai pour répondre aux fluctuations d’une production en flux tendu. Les cadres quant à eux — dont les effectifs ne sont pas à négliger — doivent en plus de leur cœur de métier maîtriser des compétences annexes, telles que l’anglais par exemple, afin d’échanger avec des interlocuteurs désormais internationaux.
À cela s’ajoute la sous-traitance d’une partie de leurs activités auprès de consultants implantés à proximité, ce qui implique que des ressources humaines qualifiées soit localement disponibles. En somme, les compétences, mais surtout la flexibilité de la main-d’œuvre, restent constitutives de l’attractivité du territoire.
Pour conclure, selon vous, pourquoi l’usine d’assemblage des moteurs de Renault Trucks est-elle toujours implantée à Vénissieux ?
C’est une bonne question. Il m’est difficile de vous avancer précisément les raisons qui poussent Volvo à maintenir son usine moteurs à Vénissieux, mais plusieurs pistes se dessinent. D’abord, comme évoqué, le site de Vénissieux est implanté au sein d’un territoire à l’héritage industriel fort, qui offre encore des avantages malgré sa déstructuration.
L’usine bénéficie certes d’un tissu industriel local plus réduit qu’autrefois, mais il demeure important au regard de ceux observés dans le reste de la France. Cette proximité avec les autres acteurs industriels et les centres de recherche favorise des synergies. On peut par exemple citer le cluster CARA, qui accompagne les mutations des systèmes de transport et dont le président fait partie du comité de direction de Renault Trucks.
Ensuite, l’agglomération lyonnaise offre des avantages logistiques majeurs — notamment l’accès à des réseaux de transport performants pour l’acheminement des marchandises — ainsi que la présence d’un bassin d’emploi et de compétences conséquent. Outre l’usine moteurs, le site industriel dans son ensemble présente une importante surface foncière à valoriser. Le constructeur a ainsi décidé d’y implanter son futur centre mondial de distribution de pièces de rechange.
Enfin, le maintien des activités de Renault Trucks dans l’agglomération lyonnaise peut aussi s’expliquer par une importante intervention des pouvoirs publics. Le site a ainsi bénéficié de crédits d’impôt recherche et de compétitivité et d’emploi. L’entreprise a de plus bénéficié d’aides de la région Auvergne-Rhône-Alpes pour investir dans des cellules d’essai moteurs.
Plus largement, ces dynamiques de soutien sont aussi portées par le gouvernement, dont les initiatives pour accompagner les nouvelles formes d’industrie se multiplient (France Relance, France 2030, Territoires d’industrie, etc.
À voir : Qui a tué l’industrie française ? — Documentaire France Télévision (2025)
Étude
Veille stratégique - synthèse pour les élus.
Article
Si l’IA peut automatiser des tâches répétitives et libérer du temps pour des activités plus créatives, elle menace également de nombreux emplois.
Interview de Alexandre Monnin
Directeur du POPSU Transition Nice Côte d'Azur, Membre du comité scient. de CY École de design et France Villes et territoires Durables
Arrivés aux limites du système terre, et si nous nous intéressions maintenant à cet espace oublié : ce qui est à garder, ce qui reste ?
Article
Découvrez nos sept leviers à actionner pour consolider l’économie de votre territoire et améliorer sa soutenabilité !
Article
Le défi de la transition économique est immense, complexe, car il implique des transformations des activités et des modèles.
Article
Entre soutenabilité et exploitation des ressources, chaque décision ouvre la porte à un dilemme !
Interview de David Le Bras
Délégué général de l’Association des directeurs généraux des communautés de France
Et si… la transformation écologique devenait la matrice des politiques intercommunales ? Retour sur cette réflexion collective.
Dossier
Ce dossier donne de premières clefs pour interroger de manière lucide les leviers de transformation de nos entreprises et de leurs modèles.
Article
La pollution de l'eau pourrait coûter très cher à la société.